Optimierung der Torgröße und Lage in einer Lotionspumpen-Spritzgussform Die Formflussanalyse umfasst einen systematischen Prozess der Simulation, Analyse und Designanpassungen. Hier finden Sie eine Schritt-für-Schritt-Anleitung zum Erreichen dieser Optimierung:
1. Definieren Sie Projektziele und -kriterien:
- Definieren Sie zunächst klar die Ziele und Kriterien für die Lotionspumpen-Spritzgussform. Berücksichtigen Sie Faktoren wie Teilequalität, Zykluszeit, Materialverbrauch und Kostenbeschränkungen.
2. Materialdaten sammeln:
- Erhalten Sie genaue Materialdaten für das spezifische Kunststoffharz, das im Spritzgussprozess verwendet werden soll. Dazu gehören der Schmelzflussindex (MFI), die Viskosität, die thermischen Eigenschaften und andere Materialeigenschaften.
3. Modellerstellung:
- Erstellen Sie ein detailliertes 3D-Modell des Lotionspumpenteils und der Spritzgussform, einschließlich Hohlraum, Kern, Kühlkanäle und Angusssystem. Stellen Sie sicher, dass das Modell die beabsichtigten Produktionsbedingungen genau wiedergibt.
4. Simulationsaufbau:
- Verwenden Sie eine Moldflow-Analysesoftware, um die Simulation einzurichten. Definieren Sie die Parameter des Spritzgussprozesses wie Einspritzdruck, Temperaturprofile und Abkühlraten. Geben Sie die Anschnittpositionen und die anfänglichen Anschnittgrößen an.
5. Erster Simulationslauf:
- Führen Sie die erste Formflusssimulation mit den ausgewählten Anschnittpositionen und -größen durch. Analysieren Sie die Ergebnisse, einschließlich Füllzeit, Druckverteilung, Bindenähte und Lufteinschlüsse. Identifizieren Sie potenzielle Probleme oder Bereiche mit Verbesserungsbedarf.
6. Gate-Standortanalyse:
- Bewerten Sie die Eignung der ausgewählten Torstandorte. Berücksichtigen Sie Faktoren wie das ausgewogene Füllen von Hohlräumen, die Vermeidung kosmetischer Mängel und die Minimierung der Auswirkungen von Bindenähten. Passen Sie die Torpositionen nach Bedarf an.
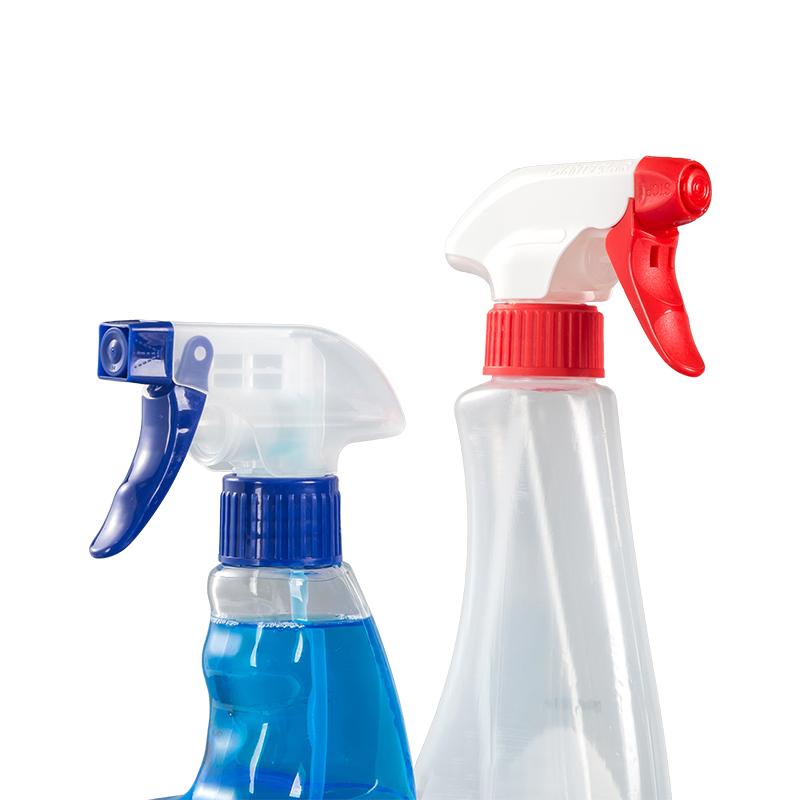
7. Gate-Größenanalyse:
- Analysieren Sie die Auswirkung der Anschnittgröße auf den Injektionsprozess. Erhöhen oder verringern Sie die Anschnittgrößen in nachfolgenden Simulationen schrittweise, um die optimale Größe zu finden, die Füllzeit, Druck und Materialfluss in Einklang bringt, ohne Fehler zu verursachen.
8. Auswahl des Tortyps:
- Wählen Sie abhängig von den Ergebnissen der Angussgrößenanalyse den geeigneten Angusstyp aus, z. B. einen Angussanguss, einen Kantenanguss oder einen Fächeranguss. Der Angusstyp beeinflusst, wie das Material in die Kavität gelangt, und kann sich auf die Teilequalität auswirken.
9. Optimierung des Läufersystems:
- Optimieren Sie das Design des Angusssystems, um eine gleichmäßige Materialverteilung in allen Hohlräumen sicherzustellen. Passen Sie die Abmessungen und Konfigurationen der Läufer an, um Materialverschwendung und Druckabfall zu minimieren.
10. Kühlkanalanalyse:
- Bewerten Sie den Einfluss der Torposition und -größe auf die Kühleffizienz. Stellen Sie sicher, dass die gewählte Anschnittkonfiguration die Wirksamkeit der Kühlkanäle nicht beeinträchtigt. Passen Sie bei Bedarf die Platzierung des Kühlkanals an.
11. Iterative Simulation:
- Führen Sie iterative Simulationen durch und nehmen Sie basierend auf den Analyseergebnissen schrittweise Anpassungen an Anschnittpositionen und -größen vor. Verfeinern Sie das Design weiter, bis die gewünschten Kriterien, wie ausgewogene Füllung und minimale Mängel, erfüllt sind.
12. Endgültige Validierung:
- Führen Sie eine abschließende Formflussanalyse durch, um die optimierte Angussgröße und -position zu validieren. Bestätigen Sie, dass der Entwurf die vordefinierten Projektziele und -kriterien erfüllt.
13. Dokumentation und Berichterstattung:
- Dokumentieren Sie die Ergebnisse, einschließlich der gewählten Anschnittkonfiguration, Simulationsdaten und etwaiger Designanpassungen. Erstellen Sie einen Bericht, der den Optimierungsprozess und seine Ergebnisse zusammenfasst.